Процесс производства и технология Н+Н
Процесс производства и технология Н+Н
Историческая справка
Метод промышленного производства автоклавных ячеистых бетонов был разработан в 30 годы прошлого века. Технология, разработанная шведским инженером Эрикссоном в 1929 году, стала известна под маркой Ytong (Итонг). Чуть позже в 1934 году появилась вторая технология, предложенная финским химиком, профессором Леннартом Форсэном и шведским инженером Иваром Эклундом. Эта технология получила название Siporex (Сипорекс).
Обе технологии очень похожи, используют автоклавы, разница лишь в том, при производстве по методу Ytong в качестве основного вяжущего материала используют известь, а по технологии Siporex - цемент, поэтому готовый продукт в первом случае часто называют газосиликат, а во втором - газобетон. В настоящее время все производители автоклавных ячеистых бетонов используют как известь, так и цемент, поэтому в дальнейшем мы будем пользоваться наиболее распространенным термином - автоклавный газобетон.
Технология изготовления автоклавного газобетона Н+Н
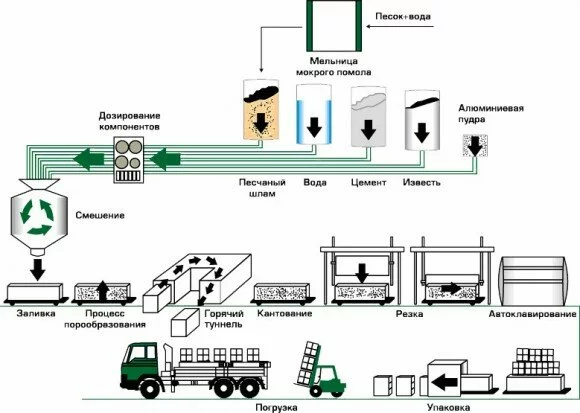
Газобетон производится из экологически чистого минерального сырья: кварцевого песка, цемента, извести, алюминиевой пудры и воды. На первом этапе производства кварцевый песок перемалывается в песочный шлам, который затем смешивается с остальными компонентами для образования ячеистобетонного раствора.
Рецепт смеси во многом определяет характеристики готового продукта, поэтому тщательно разрабатывается и контролируется. Автоматическая система управления весовым дозатором и смесителем является сердцем линии по производству автоклавного газобетона, она связана с центральным компьютером завода, где хранятся все параметры сырья и рецептуры. Каждый новый замес сравнивается с предыдущим, и возможные незначительные отклонения автоматически устраняются. Переход с одной рецептуры на другую занимает минимум времени.
Готовый раствор заливают в формы, где начинается химическая реакция с выделением водорода (в качестве газообразователя выступает алюминиевая пудра), образующиеся при этом пузырьки газа вспучивают раствор, и последний распределяется вокруг пузырьков, образуя равномерную ячеистую структуру.
После формирования массива-сырца газобетона, он на несколько часов помещается в специальную камеру с подогревом для набора предварительной прочности (созревания), необходимой для резки.
Затем массив извлекается из формы и поступает на резательную установку, где разрезается в двух направлениях на готовые блоки, заданных размеров. В резательной установке используются сильно натянутые тонкие стальные струны, которые гарантируют очень высокую геометрическую точность готовых блоков с возможной погрешностью +/- 1мм.
После этого нарезанные блоки на специальных вагонетках поступают в автоклав, где они проходят термическую обработку водяным паром при температуре 175-200°С и давлении 8-13 атмосфер. Все перечисленные выше компоненты ячеистобетонного раствора при автоклавной обработке вступают в реакцию друг с другом и образуют уникальную кристаллическую структуру, новый минерал - доберморит, за счет которого повышается прочность блока и в несколько раз уменьшается усадка.
В результате описанного выше процесса производства на выходе получается искусственно созданный белый камень, который не содержит ни песка, ни цемента, ни извести, ни алюминиевой пудры.
На последнем этапе готовые блоки поступают на линию упаковки: проходят через разрывную машину, устанавливаются на поддоны и упаковываются. Упаковочный автомат набрасывает на партию блоков пакет из усадочной пленки, который обжимается при помощи газового подогрева по форме блоков.
Далее готовые упакованные в пленку блоки транспортируются погрузчиками на склад готовой продукции.
Весь производственный процесс настолько компьютеризирован и автоматизирован, что одна рабочая смена составляет меньше 10 человек.
|